スパウト装着製品の製造販売
環境にやさしいスパウトパウチで時代のニーズに柔軟に応える。
スパウトパウチの豊富なラインナップでお客様の用途に合わせた提案を行います。立体容器にスパウトを装着することにより、内容物の流出入をコントロールする機能を加えることができます。何度も使用でき、中身を無駄なく使い切ることができるため、プラスチック使用量が少なく、輸送効率が高いことから、環境に配慮した「地球にやさしい」製品です。
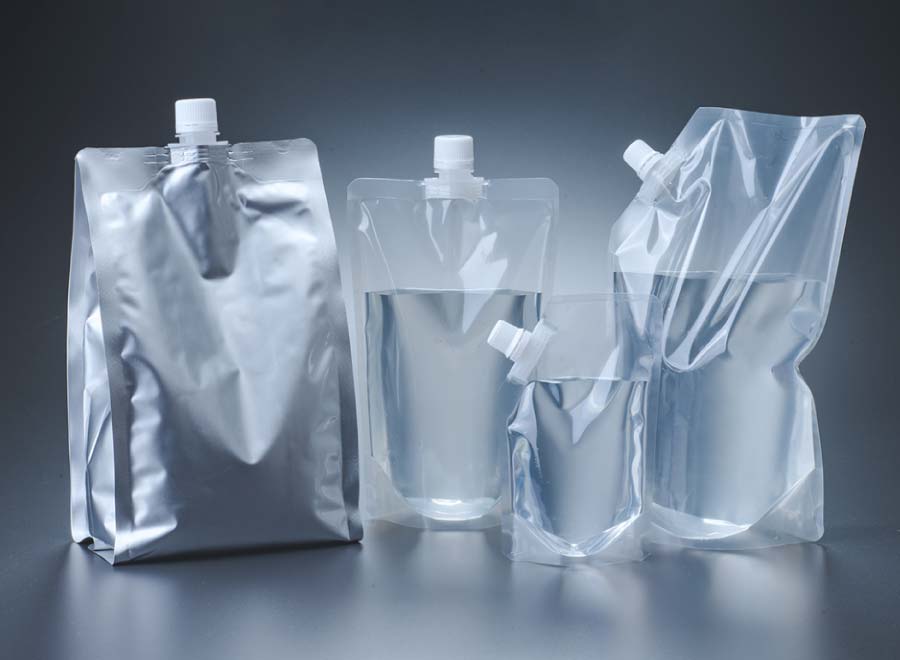
中身や用途に合わせて四角タイプ(スタンドパウチ、ガゼットパウチ)、三角タイプ(フラットパウチ)、スパウト口径、スパウト位置をお選びいただけます。別注品もご用意しております。

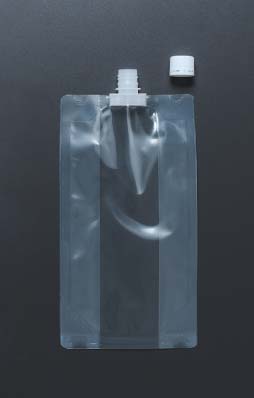
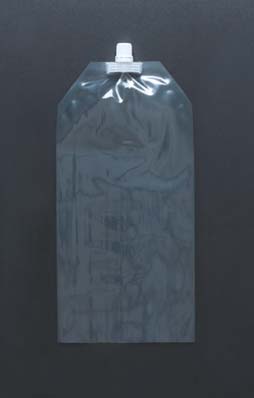
送料元払いで全国発送可能。当日午前中に発注いただければ翌日出荷、サンプルも無料でご用意します。
※決済確認後に発注完了となります。
スパウト袋は、フィルムタイプで柔軟性があります。ボトル容器より樹脂使用量が少なく、内容物を最後まで絞り出すことができ、無駄なく使えます。
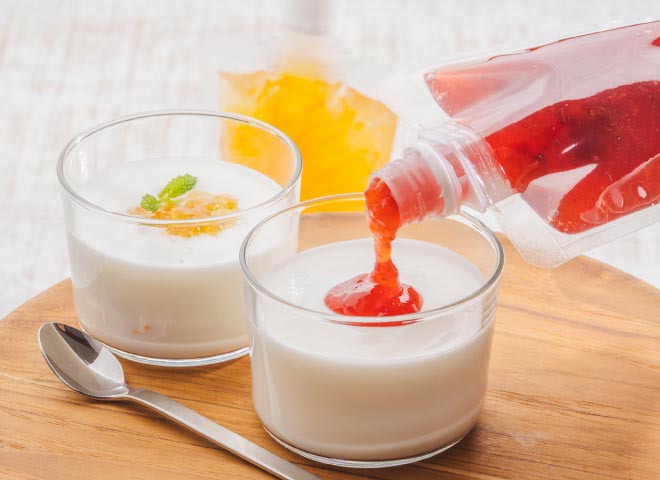
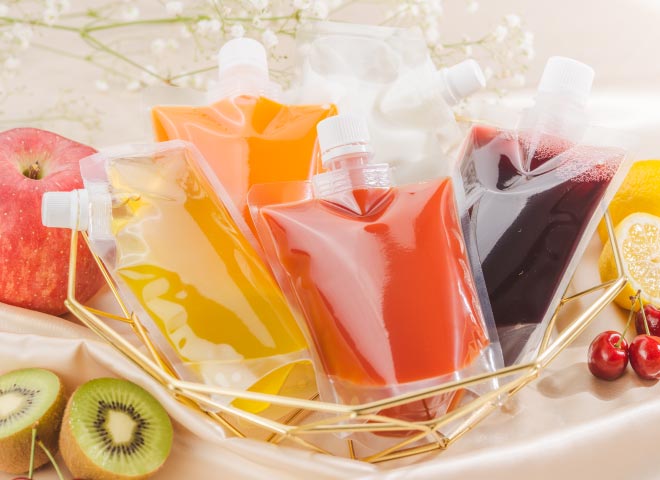
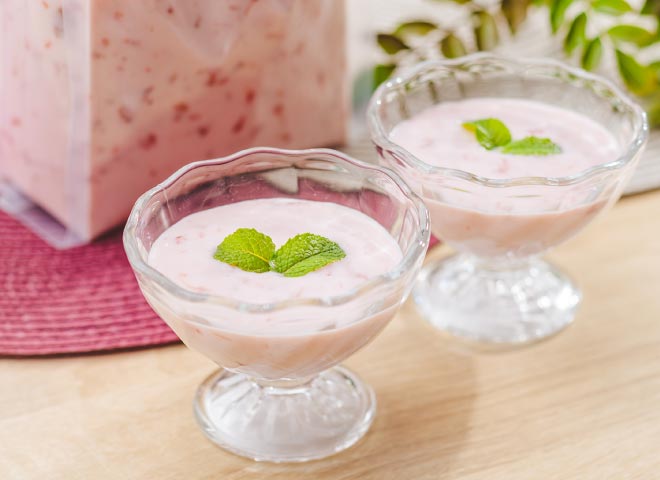
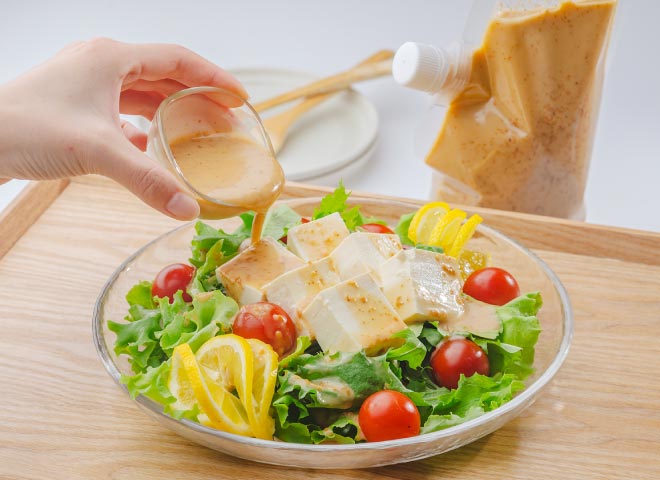
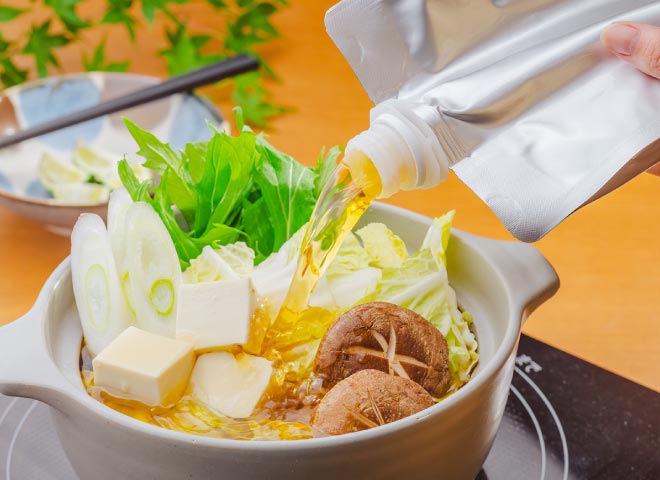
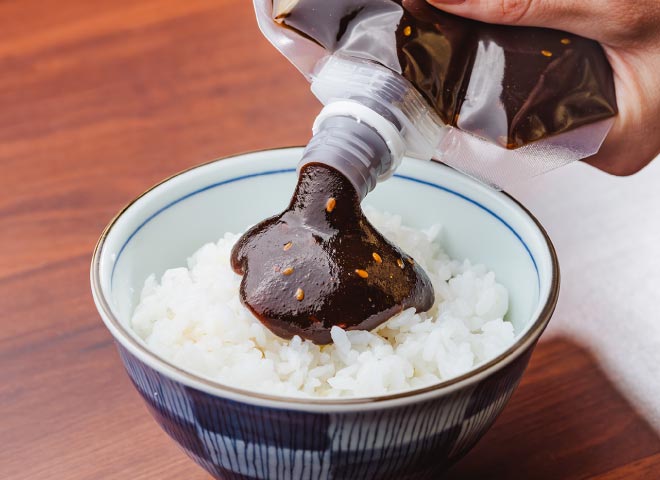
「スパウト」とは、ポリエチレンを使用して樹脂成型された口栓のことを指します。また、キャップはスパウトの径に応じて、ポリエチレンやポリプロピレン製のものが使用されます。なお、シール面に使われるシール材はLLDPEに限定されます。当社では下記のサイズをご用意しております。
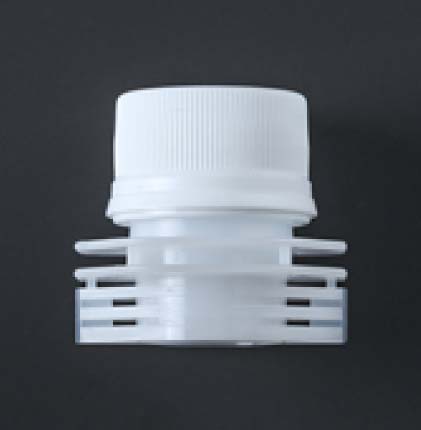
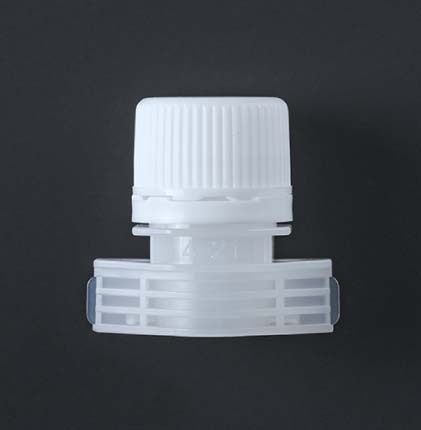
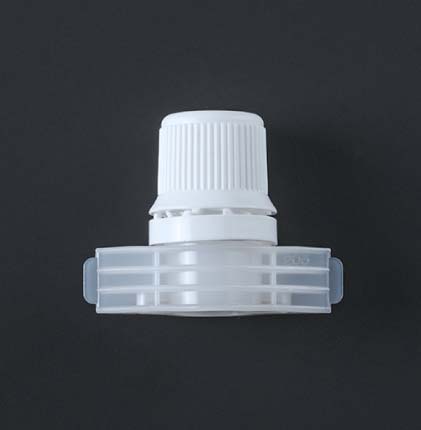
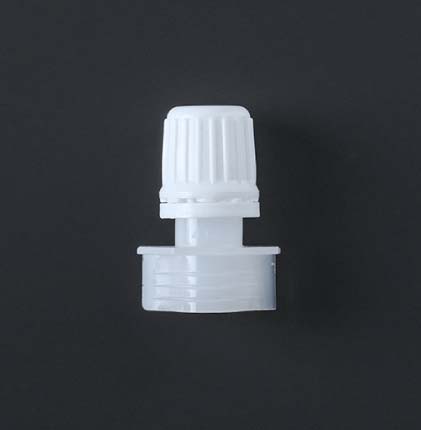

当製品は、共押出しチューブフィルムを使用しており、サイドシールが必要なく、内容物を最後まで使用できます。
また、当社の三角袋は底が開いており、80℃で30分間のボイル加熱処理に耐えられます。
また、マチがない持ち手により、手に違和感がなく絞りやすいのが特徴です。
水冷インフレーション法で製造された5層のナイロンチューブを使用しています。このチューブは、ナイロン樹脂とポリエチレン樹脂を多層ダイから一緒に押し出し積層したフィルムで、柔軟性をもち、透明性や光沢感に優れます。
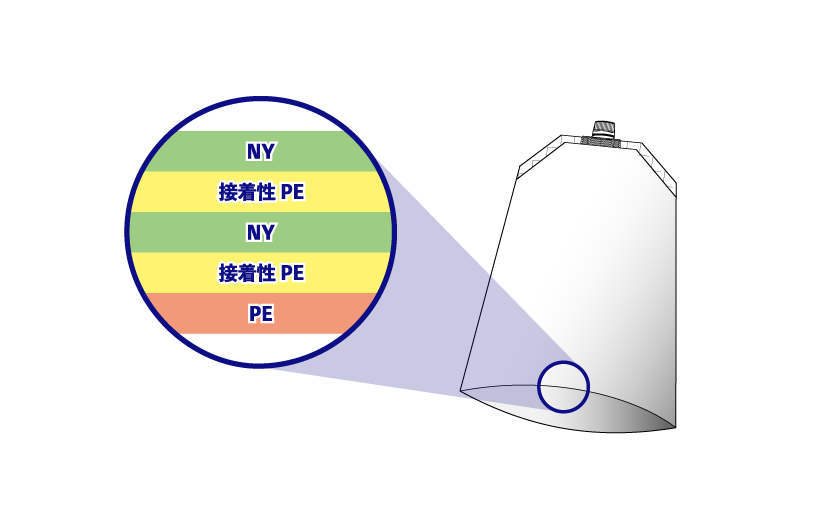
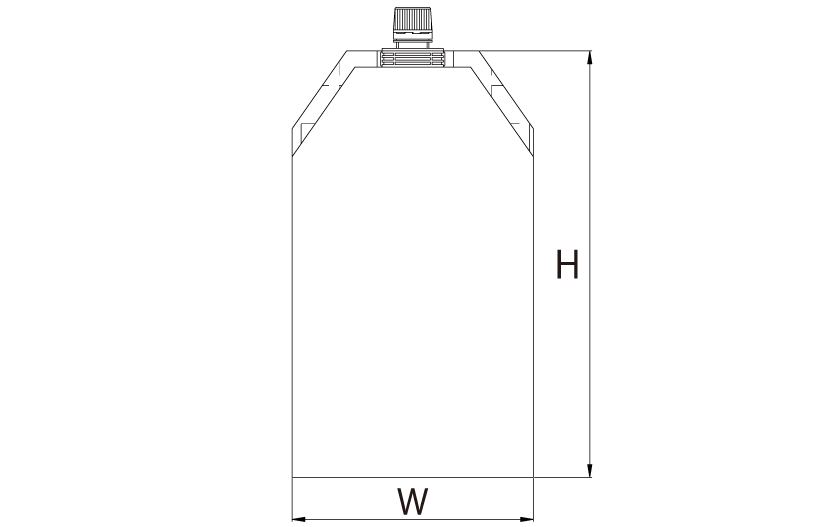
品番 | サイズ W×H×D | 目安容量 | 入数 | スパウト |
---|---|---|---|---|
VSPN010 | 0.1×150×310/335㎜ | 1kg | 500枚 | 16mmΦ |
VSPN010 | 0.1×150×310/330㎜ | 1kg | 700枚 | 9.5mmΦ |
VSPN005 | 0.1×150×265/290㎜ | 500g | 500枚 | 16mmΦ |
VSPN005 | 0.1×150×265/285㎜ | 500g | 700枚 | 9.5mmΦ |
VSPN003 | 0.1×120×200/225㎜ | 300g | 600枚 | 16mmΦ |
VSPN003 | 0.1×120×200/225㎜ | 300g | 600枚 | 8.7mmΦ |
ナイロンフィルムやLLDPEフィルムを使用したラミネート袋を使用しています。これは、異なるフィルムを貼り合わる事によって、お互いの特性を生かし、袋の中身を保護します。特に、ナイロンフィルムとLLDPEフィルムを使用したラミネート袋は、冷凍・冷蔵で流通する商品に適しています。
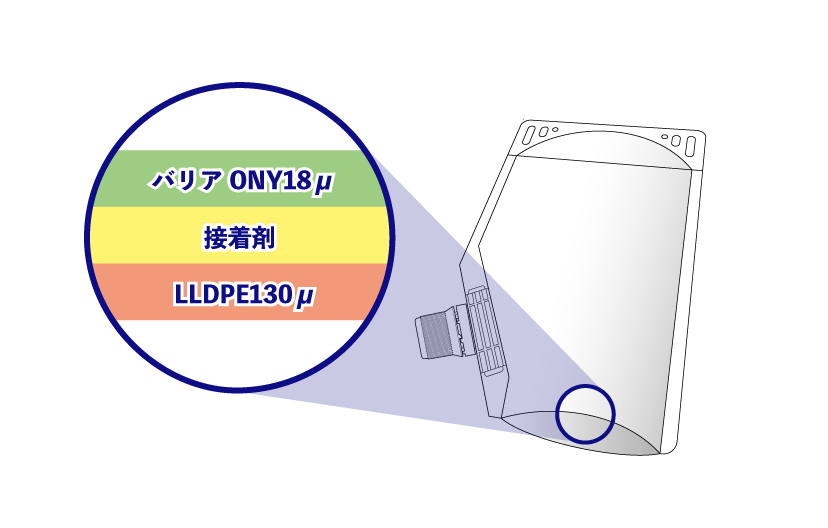
バリアタイプのナイロンフィルムを使用しており、強靭で食品の保存に適しています。袋本体には口栓が付いており、開口部から漏斗などで簡単に充填することができ、食品を封入した後はそのまま湯煎可能で、手軽に殺菌可能なため、オリジナルのソースやたれの製造に適しています。
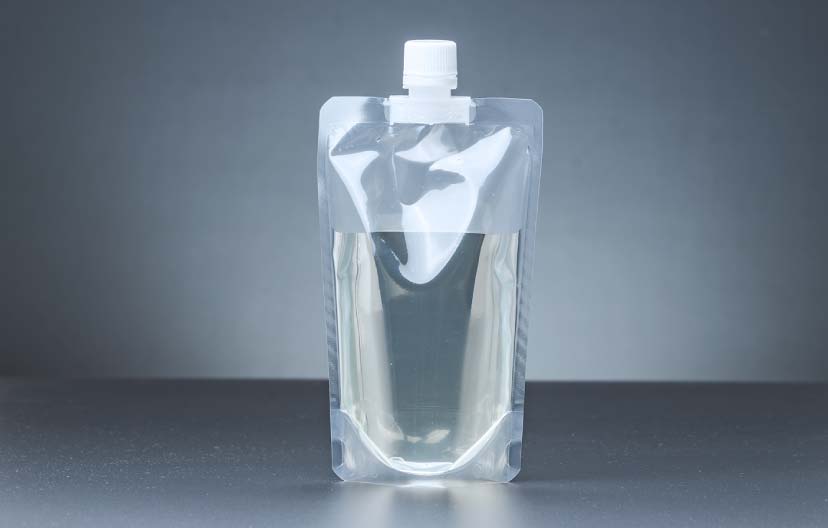
スパウトセンター装着品は、スパウトの口から内容物を充填し、同梱のキャップを締めて密封します。スパウトコーナー装着品は、フィルムの天井開口部から内容物を充填し、フィルムの開口部をシールして密閉します。
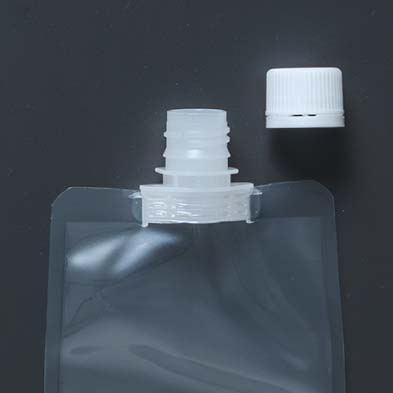
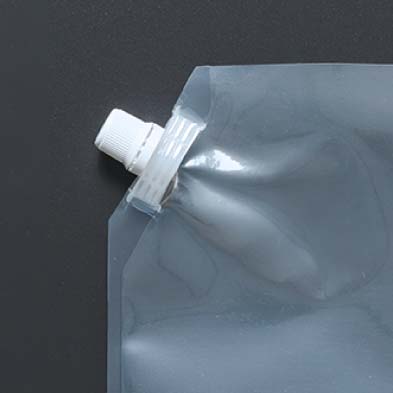
-
- バリアナイロンタイプ
- バリアナイロンとLLDPEをラミネートした2層フィルムです。強靭で、ガスバリア性に優れています。主にゼリー飲料などの飲料製品を包装するために使用されます。
-
- ハイバリアタイプ
- 透明蒸着PET、ナイロン、LLDPEをラミネートした3層フィルムです。バリアナイロンタイプよりさらに高いガスバリア性を備えており、食品劣化を防ぎます。主に一般的な食品(タレ、ドレッシング、ソースなど)を包装するために使用されます。
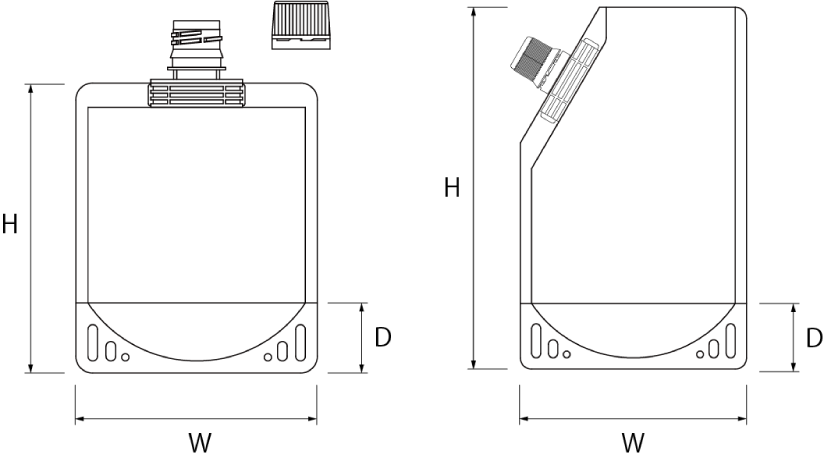
品番 | 材質 | サイズ W×H×D | 目安容量 | 入数 | スパウト |
---|---|---|---|---|---|
SSPS001 | バリアナイロンタイプ | 100×120×29mm | 100ml | 750枚 | 口内径16mmΦ、センター装着(キャップは同梱) |
SSPS002 | バリアナイロンタイプ | 110×140×33.5mm | 200ml | 750枚 | 口内径16mmΦ、センター装着(キャップは同梱) |
SSPS003 | バリアナイロンタイプ | 110×180×33.5mm | 300ml | 500枚 | 口内径16mmΦ、センター装着(キャップは同梱) |
SSPC0015 | バリアナイロンタイプ | 100×160×29mm | 150ml | 600枚 | 口内径9.5mmΦ、コーナー装着(キャップ付き) |
SSPC0025 | バリアナイロンタイプ | 100×200×29mm | 250ml | 500枚 | 口内径9.5mmΦ、コーナー装着(キャップ付き) |
SSPS005 | ハイバリアタイプ | 140×220×40mm | 500ml | 250枚 | 口内径16mmΦ、センター装着(キャップは同梱) |
SSPC005 | ハイバリアタイプ | 140×220×40mm | 500ml | 300枚 | 口内径9.5mmΦ、コーナー装着(キャップ付) |
SSPC005 | ハイバリアタイプ | 140×220×40mm | 500ml | 360枚 | 口内径16mmΦ、コーナー装着(キャップ付) |
SSPS010 | ハイバリアタイプ | 170×270×45mm | 1000ml | 250枚 | 口内径16mmΦ、センター装着(キャップは同梱) |
SSPC010 | ハイバリアタイプ | 170×270×45mm | 1000ml | 300枚 | 口内径9.5mmΦ、コーナー装着(キャップ付き) |
袋の四隅に熱シールされたピラーと呼ばれる支柱を設けており、袋形状がくずれにくく排出性に優れます。従来品のスタンドタイプに比べ面積効率約40%UP。コンパクトな見た目に反して大容量。サイドガゼットタイプのスパウトパウチです。
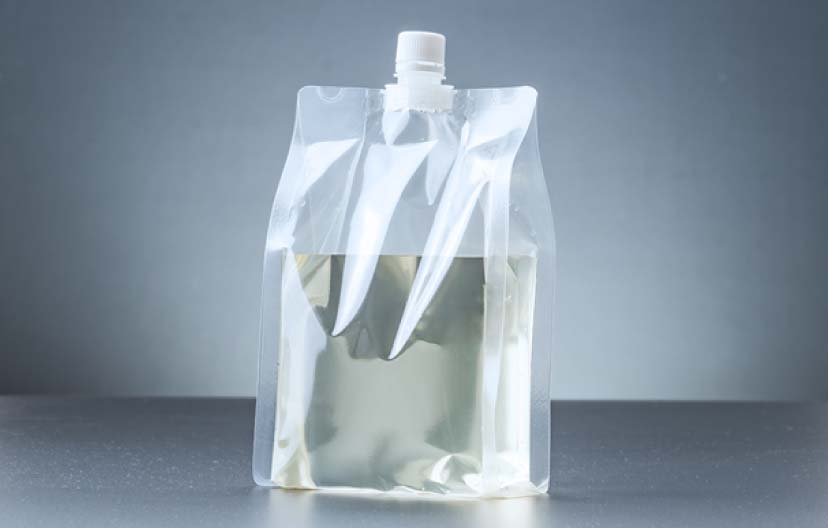
PETフィルムとバリアナイロン、LLDPEをラミネートした3層フィルムです。高い透明度を有し強靭でガスバリア性に優れています。主に、内容物は一般的な食品(タレ・ソースが多いです)
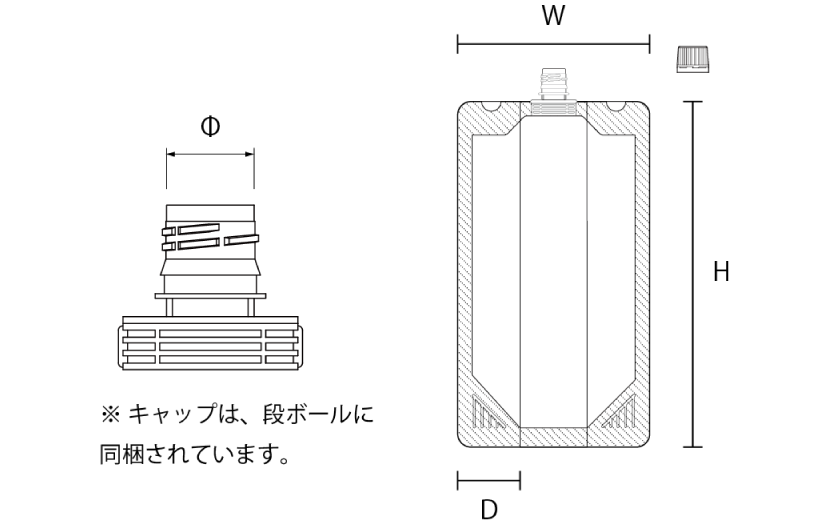
品番 | サイズ W×H×D | 目安容量 | 入数 | スパウト | キャップサイズ |
---|---|---|---|---|---|
CSPS020 | 160×310×50㎜ | 2000ml | 250枚 | 口内径16mmΦまたは21mmΦ | 16mmΦ、21mmΦ |
CSPS010 | 140×260×40㎜ | 1000ml | 250枚 | 口内径16mmΦまたは21mmΦ | 16mmΦ、21mmΦ |
規格品に加え、お客様のご要望に合わせたさまざまな容量や用途に対応した製品を提供しています。また、口内径が8.7mmφ、9.5mmφ、16mmφ、21mmφの4種類のスパウトを取り揃えています。受注時期や数量によるリードタイムはご相談ください。
※弊社のスパウト装着製品は食品用途となります。食品外の使用については、お客様の責任において、ご使用ください。
※内容物が酸性度の高いもの、発酵性のものには使用できません。
※輸出向けは不可とさせていただきます。
※サイズ、容量は若干差異があります。
※製品の仕様は予告なく変更することがあります。